Designing an Abrasive Blast Room
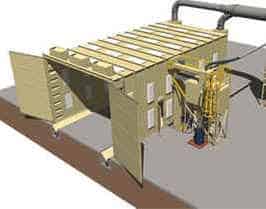
Abrasive blasting has been around for as long as man could throw a mineral abrasive, such as silica sand on to an object. The reasons for the surface preparation vary from removing an existing coating to preparing the surface to accept a new coating. The idea is simple and the industry was born with the advent of the air compressor.
An abrasive blast room is the core to any modern abrasive blast system.
Confining the blasting operation to a controlled clean environment enables efficient abrasive recycling.
The design criteria required for a properly sized blast room system includes the size of the largest work piece, weight of the largest work piece, material handling method, the number of hours of blasting per day, and the base material of the work piece.
Each of these items needs to be addressed in order to finalize the configuration of the blast room.
What Size Should It Be?
The size of the largest piece will determine the dimensions of the blast room enclosure. The width of the room is determined by adding 4-5 feet on each side of the work piece. This space is required for the blast operator to maneuver around the part and blast the part from various angles.
The height of the blast room is also determined by the work piece height; but the material handling of the part must also be considered. For example, if a work car on a track is the material handling method, then the height of the work car must be taken into consideration to determine proper clearance of the blast room roof panels. Again, a 4-5 foot clear area will be required for the blast operator or up to 7 feet clear if the operator will walk on top of the part while blasting (e.g.-a tank in the railcar industry).
Likewise the length of the blast room is determined by adding 4-5 feet on each end of the work piece to allow for operator clearance.
Proper planning and design of the blast room results in the best built rooms suited to your specific needs. ABS Blast has the experience and expertise needed to assist you in all steps of your blast room design and build. Let our quality of work speak for itself.